Neil Heeke, technical expert and new business development, Schott North America, Inc shares his thoughts on how hermetic glass-to-metal seals can provide a whole-system lidar packaging solution that brings down costs while also boosting performance.
The first lidar systems installed on cars were large systems that used individual lasers, detectors and mechanical scanners to create 3D images for assisted or autonomous driving. With the development of solid-state arrays and active beam steering, most of today’s lidar systems incorporate at least some solid-state parts because these chip-based components can improve reliability and lower cost. Although there is still significant progress to be made, a solid-state system without moving parts is the ultimate goal.
Schott’s hermetic glass-to-metal seals can protect lidar systems from harsh conditions, such as extreme temperatures, moisture or pressure. For systems that rely on solid-state technology, packaging multiple components in a single hermetic package can save money, make the system easier to manufacture, and keep the system running at top performance over its entire lifetime.
Is a hermetic seal really needed?
There is a common misconception that the electronics used in automotive lidar systems don’t need hermetic packages because they already have a plastic enclosure or are potted with a protective polymer like epoxy or silicone. Although these protective measures can keep out moisture, they don’t work well with optical systems because there isn’t a way for light to enter and leave the package.
It’s also easy to think that optical components such as vertical emitting lasers or CMOS imaging chips don’t need additional packaging because they tend to be manufactured with moisture protection. However, lidar applications expose these components to extremely harsh conditions that are often not present in other applications. Even lidar systems installed inside the headlamp area or in the car’s interior — rather than on the outside of the car — experience large temperature swings. If the seal is not robust enough to withstand the pressure increase at the hottest part of the day, the resulting vacuum created during cooling draws in water through the leak paths where it can lead to condensation, corrosion, shorting, and eventually system failure. A properly designed glass-to-metal sealed encapsulation keeps this from happening.
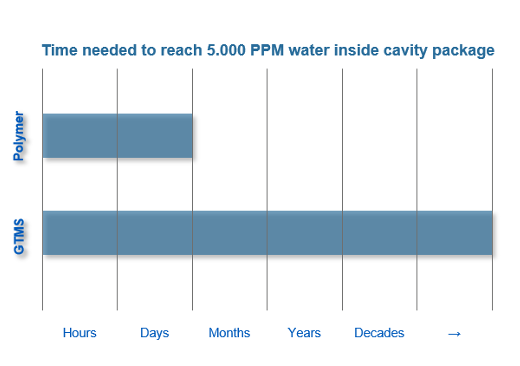
The move toward solid-state means that more lidar systems are relying on MEMs mirrors for scanning. For this component, a hermetic glass-to-metal seal can be used to create a vacuum inside the package that can be maintained for years. The vacuum eliminates air resistance, which increases the range and speed of these components, enabling lidar systems to capture information from a larger area.
Why seal the whole system?
Although each component can be hermetically sealed individually — and this is often the approach when size constraints aren’t an issue — this extra packaging takes up unnecessary room and makes it difficult to align the optical components. With glass-to-metal sealing, an extremely compact system can be precisely built and enclosed completely in a hermetic package. This approach is more economical because the integration of the optics is much more straightforward while also extending the life of the product because more of the optical chain is protected.
Packaging the entire system together also eases laser alignment because there’s no need to go through a lens or window on the wall of a hermetic package, for example. This eliminates challenging interconnection issues and takes away the need for realignment and recalibration. Once all the components are together, they can be hermetically sealed in a way that maintains alignment for the lifetime of the product.
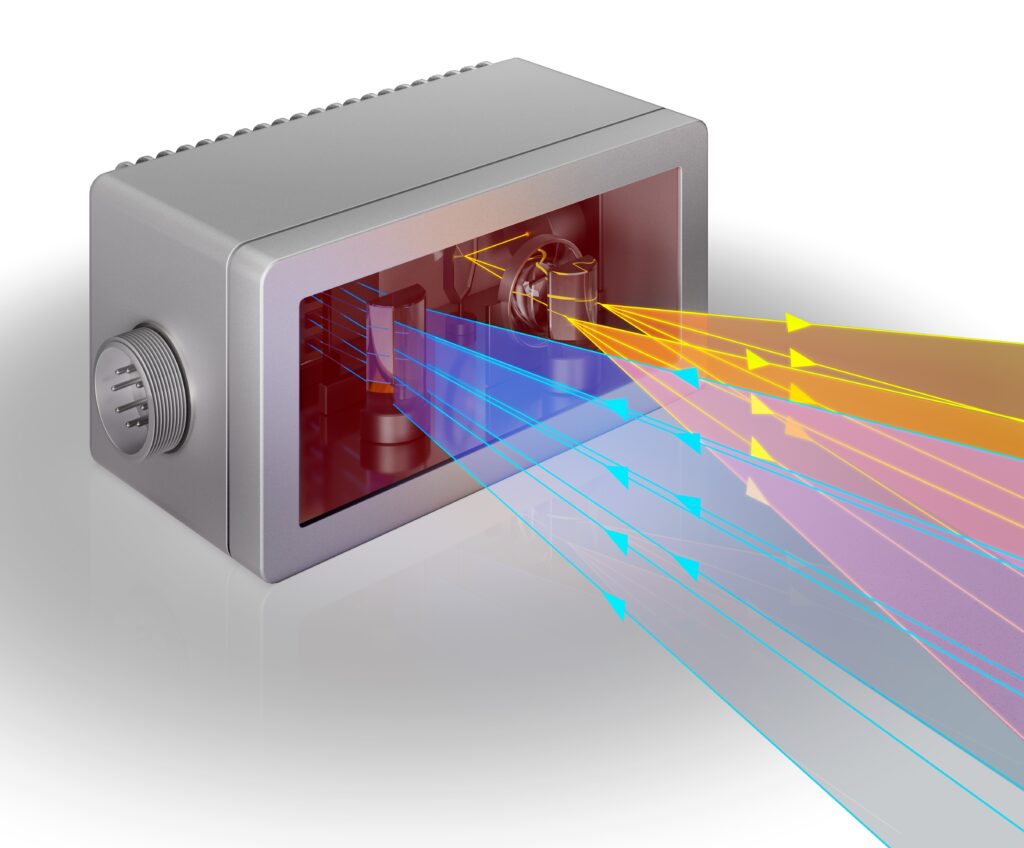
Drawing on decades of experience in glass-to-metal seals, Schott can provide solutions that are customized to meet the needs for a specific lidar system. We offer various ways to bring electrical signals in and out of the package and options to incorporate optical windows that provide an optical path through the package walls. It’s also possible to control what’s inside the hermetic package. These include options for dry air, vacuum conditions, nitrogen or helium. By partnering with Schott, lidar system manufacturers gain access to years of expertise and a team that will work with them from concept development to prototyping, testing and manufacturing scale-up. Learn more from the product website.
Interested in more on hermetic packaging? Discover how to boost the lifetime and performance of automotive lidar systems with hermetic packaging, here.