Wouter Remmerie of CFD specialist AirShaper addresses the important but under-publicized role of water and dirt management on vehicles, how it can be simulated and the impact it has on the operation of ADAS and AD sensors.
Why do some vehicles seem to get dirtier than others? While some owners are not the best at keeping their vehicles clean, aerodynamics also has a major role to play. To find out the physics behind vehicle water and dirt management and how simulation can help, we spoke to our two partners, Nextflow Software and A2Mac1.
Water management across a vehicle’s body encompasses everything from designing efficient windshield wipers to adding aerodynamic devices to control the exterior airflow around a vehicle.
“It’s essentially all about the interaction of liquid with the exterior surface of the car,” explains Vincent Keromnes, dynamic benchmarking domain leader at A2Mac1. “This can include rain, water wading and water injection. It’s crucial to monitor where water can get through on a vehicle. If it accumulates in the engine bay, battery pack or on a camera, it can cause major issues.”
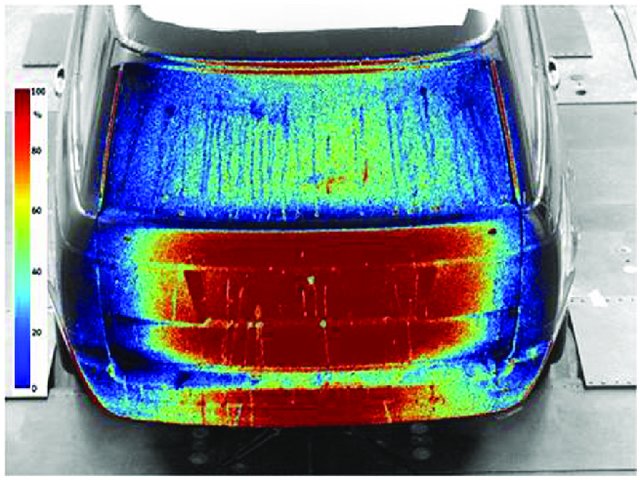
Dirt, debris, stones and other contaminants also need to be accounted for. Due to the miniature nature of these particles, they are strongly influenced by the exterior airflow and the aerodynamic properties of the body need to be massaged in order to minimize these particles either hitting the surface or being ingested through intakes and openings.
“There are two main sources of soiling,” highlights Keromnes. “First, there is self-soiling, which is from the vehicle itself. Wherever there is flow separation, such as on the sideview mirror or at the rear of the car, a wake is generated that causes contamination. Then there is third-party soiling, which is caused by the interaction of wind, rain and dirt with other obstacles on the road.”
“The most important reason is obviously safety,” he continues. “ Also, with more ADAS systems on board modern vehicles, cameras and lidar sensors are very sensitive to dirt. Just a droplet of water on such a tiny camera can seriously affect its performance. This is becoming increasingly important as we move toward more autonomous driving. These types of devices need to stay clean or be easy to clean.
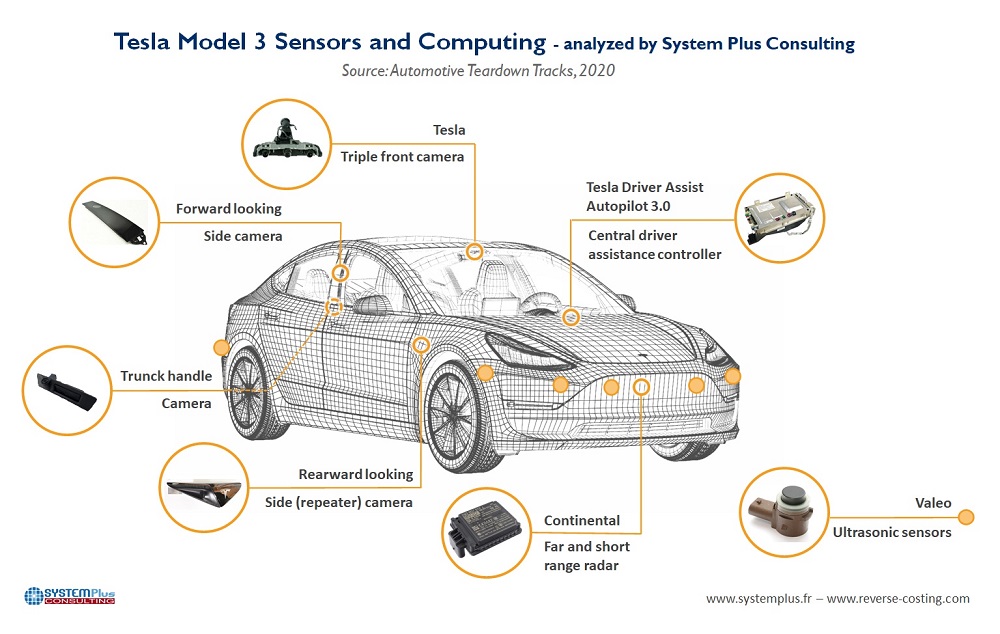
Early in a vehicle’s design process, designers will analyze the aerodynamics to control the behavior of water and dirt to keep key areas of the vehicle clean. However, in areas where this can’t be done, they have to develop systems that remove dirt and water.
For example, says Keromnes, “carefully controlled spraying techniques can be used, which are efficient and inexpensive. This has become so important that some manufacturers now have specific departments dedicated to developing these spray systems. It’s interesting to know how fast a car can get dirty, but it’s also interesting to know how fast you can clean it. Both of these can be done through simulation.”
Accurately modeling the behavior of a consistent airflow over a vehicle is challenging enough. Add in the effect of wind, the dynamics of water and the trajectories of dirt particles, and you can begin to appreciate the difficulties of simulating water and dirt.
This is why such analysis requires the combination of aerodynamic and hydrodynamic simulations. As the water droplets on the vehicle’s surface are so small, these local flow fields don’t have a major effect on the aerodynamics. Therefore, computational fluid dynamics (CFD) simulations evaluating the global aerodynamic performance of the vehicle are completed first. Then, this flow field is used for separate simulations where liquid particles are injected into the simulation to predict the forces and trajectories of water and dirt particles.
“If we need to conduct a more detailed analysis we can also add in some particle refinement algorithms. This allows us to evaluate the wettability effect such as surface tension, dynamic contact angle, etc of smaller particles in more specific areas,” notes Julien Candelier, the technical team leader at Nextflow Software.
Of course, such complex simulations require a substantial amount of computing power. “The main challenge is memory management,” highlights Candelier. “That’s why everything is modeled as a steady flow using a mean value of diversity of car wake. Even with that, we are dealing with gigabytes of data.
“To cope with this, we do some parallel computing for the liquid phase to achieve efficient simulations. For example, a full wheel soiling simulation can run in 20 hours on a regular desktop.”
More examples of aerodynamic simulation case studies can be found on AirShaper’s blog, here https://airshaper.com/blog.