In 2010, Geely Auto was just that: Geely Auto, a company that had sold 415,000 vehicles that year. By 2019, it was trading as Zhejiang Geely Holding Group having taken ownership of major names such as Volvo, Lotus, LEVC, Lynk & Co, Polestar and Proton, and had hit annual sales of 2,178,000 across its three automotive subsidiaries.
The group has research and development centers across the globe, including two in China – the main Geely Automotive Research Institute in Hangzhou and another in Ningbo. It also has the China Euro Vehicle Technology (CEVT) center in Gothenburg, Sweden, and a facility in Coventry, UK. All are focused on four main R&D pillars: universal platforms, safety first, energy diversification and automotive intelligence.
Li Li is vice president of R&D for the group, based at Hangzhou. He oversees 10,000 engineers throughout the various centers plus another 4,000 involved purely in powertrain R&D. Since joining the company from Ford in 2014, Li has been a major part of the growth of Geely, something that has required a carefully planned integration of both technology and business practices.
“First we have to have the right people. Then the process,” he explains. “That’s what Geely has been developing for several years and what differentiates us from other Chinese or global OEMs.” That process is called the new product development strategy (NPDS), which was inherited from Volvo when Geely purchased the Swedish brand in 2010. Geely has expanded its NPDS in recent years and today every single employee in the group is trained in it so they understand how models are developed.
Geely’s globalization has benefits and challenges, however. Localizing R&D in centers around the world has made some aspects easier, but at the same time employees coming from other companies need to learn the Geely way of doing things. “It’s no easy task because you need to educate people to follow a certain way of doing things and give up what they are used to. That’s very challenging, especially when this process will be applied to different organizations in different cultures,” Li notes.
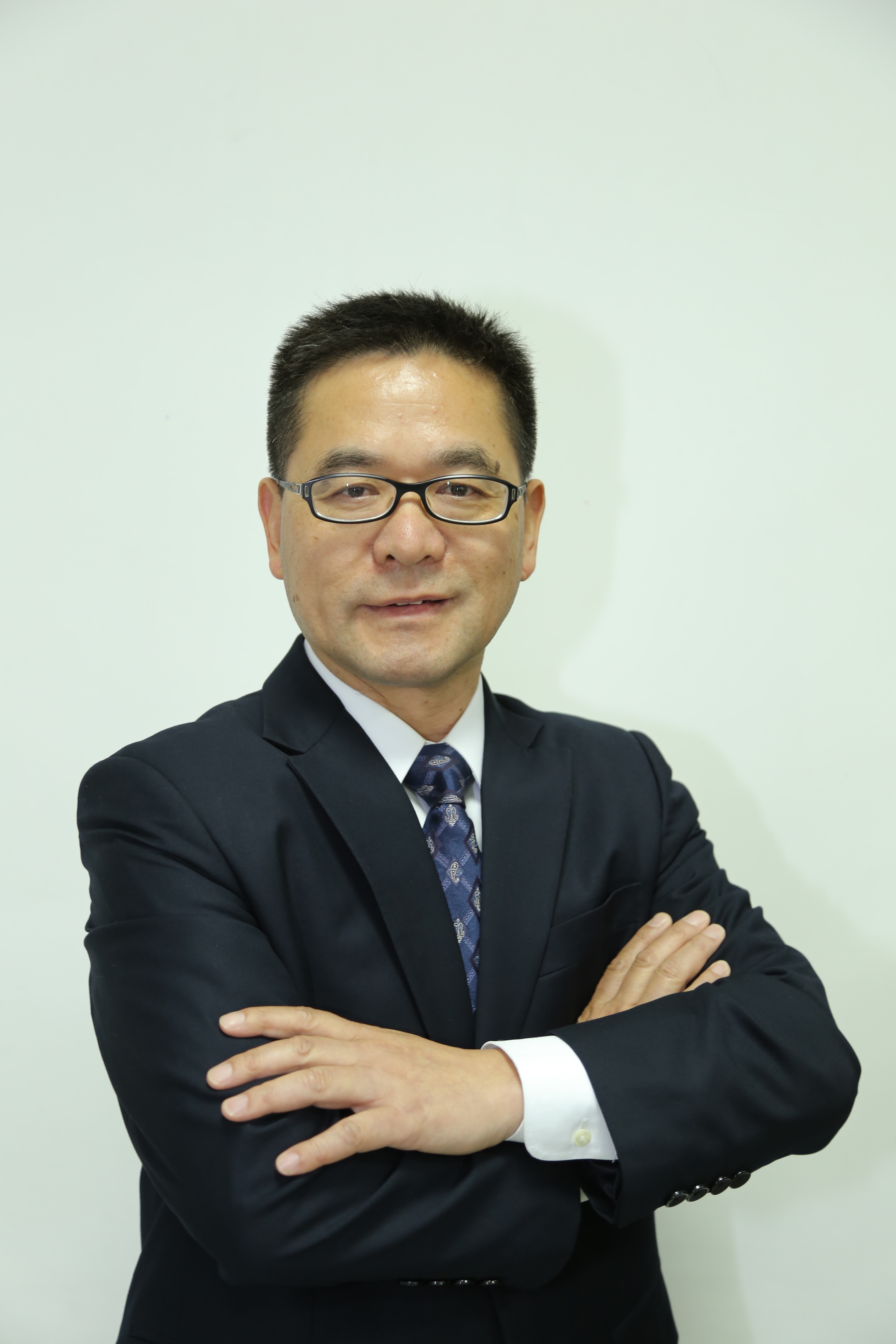
One area on which Li and his team have been focused is platform architecture – also something that has come from Volvo. “Chinese OEMs used to focus on developing vehicle lines. Geely however, through working with Volvo, has started to focus on platform architecture, like CMA [Compact Modular Architecture].”
That platform already underpins the Volvo XC40 and Lynk & Co 01, and although it’s completely capable of electrification, the group has spent the last four years developing a new EV platform called PMA, or Pure Electric Modular Architecture. “Geely has built upon the CMA platform experience and our global talents have enabled us to develop a highly sophisticated EV platform,” says Li. “We have the capability and we have the volume to support it, ensuring our new platform will be very competitive both in terms of cost to the customer and performance.”
Unlike CMA, which also has to accommodate ICE-based powertrains, Li says that PMA has been developed purely as an electric vehicle platform. “It does not have to compromise for the ICE powertrain, so the performance can be fully optimized,” he explains. The PMA has a 10-year lifetime, and Li describes the architecture as a “living process” that will also be capable of delivering full Level 5 autonomy when the time is right. “We have a roadmap that can cover Level 2 to Level 4,” comments Li. “Geely was the first OEM to introduce Level 2 ADAS in China a few years ago. Now we are trying to deliver all the technologies in our roadmap and I think we have a good strategy. We will build up a good ecosystem in this field.”
Geely is building a new proving ground to test ADAS technologies and it is also testing in a dedicated city area using V2X in partnership with the authorities in Hangzhou. Currently all its testing is up to Level 4, but Li expects to begin full Level 5 testing within three to four years. “To commercialize Level 5 might not be possible in the very near future,” he notes, “but there are certain technologies within specific areas of Level 5 autonomy that we will be testing much sooner than a complete vehicle.”
Much of that testing will be done in a virtual environment, as is a great deal of the testing at Geely. “Virtual testing can significantly reduce development time and shortens our cycle,” says Li. “It’s being used in many areas, like safety, crash, durability and stress testing.” He notes that compared with the typical 36 to 48 months required by many OEMs to develop a new vehicle model, at Geely the timeframe is notably less than 36 months.
There are plans to reduce that even further with the implementation of more CAE processes throughout the group. In addition, more simulators are being added, including a new VI-grade DiM250 being installed in 2021 at the CEVT in Gothenburg. This will be used
for vehicle development across the group, including the testing of ADAS such as blind spot detection, lane departure warning, lane keeping assist, autonomous emergency braking, adaptive cruise control and fully autonomous driving systems.
Reducing development times is crucial in an era where technology and regulations are changing faster than ever, but which area of the industry is Li most fascinated by right now? “I think the main thing I’m keeping an eye on is software development. More and more OEMs are putting a lot of effort into capability in this area. The Volvo team is extremely strong in software development and Geely will be benefiting from that as a group.”
In a difficult time for the automotive industry as a whole, what does Li see as the greatest challenge for Geely’s massive R&D department at the moment? “To find solutions that can meet ever-changing customer needs within an affordable cost structure,” he says. “That is forever the challenge.”